RECOVERING THE CONCENTRICITY ERROR AMONG DIFFERENT PRESSES WITH THE "MMP" SOFTWARE FUNCTION
The customer Nordic Label OY, based in Kirkkonummi, Finland, bought the plate mounter with the purpose to replace an old mechanical plate mounter.
The customer ordered a MIDI 600 mm machine, which was designed to mount shaftless cylinders.
The mounter is required to support all the 3 different presses they actually run, MPS 330 and 530, using the sliding cones to lock the inner bearings of the shaftless cylinders.
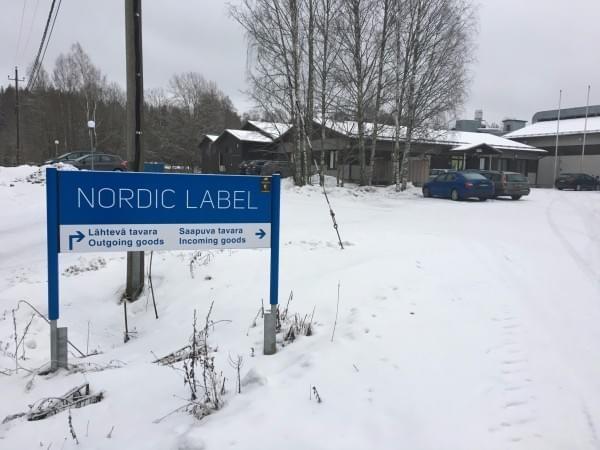
The old mounter is operating using the classical "plate on the table" process: it is not possible to do any specific registration for the press, and the mounter has a specific mechanical set up, that must fit all the presses.
As any press operator knows, each press has got its specific setup, and what is "straight" on a press may not be "straight" on another one.
In this specific case, the customer's series cylinders are showing a significate amount of T.I.R. (total indicated runout/reading) and are ouf of tolerance: from Z to Z, cylinders apparently similar are not rotating with the same concentricity.
Using the old mounter, in order to attain perfectly straight mountied plates and consequently a perfect execution of the plate on the repeat, several mounting attempts are required for any each plate, and also is often involves further adjustment of the table accordingly to compensate for this error.
This difference in the rotation concentricity is given by many possible factors that any press-room operator meet: e.g. the inner bearings tolerance on the cylinders, each cylinders manufacturer has got its mechanical tolerances, cylinders that may be worn-out, the plays on the press that the operator knows and compensates, etc.
The concentricity error is indicated on our mounter, when the sliding cones come in contact with the inner bearings, the cylinder is rotating not always concentric. Another way to look at this is the mechanical alignment of the mounter, made accordingly to the "MASTER" cylinder for the MPS 530, is not valid for other Z axis of the same press or other presses.
The second consequence is that the "closing" of the plate on the repeat is not perfect on the cylinders different from the MASTER, with a gap corresponding exactly to concentricity error (our eng. Franco Caliari is available for the trigonometric demonstration and math error calculation starting from bearings tolerance 😄 )
While the press has registration adjustments, that allows the operator to adjust the cylinder in the printing deck, the mounter is not provided with a separate mechanic regulation for each cylinder.... or simply put: the mounter cannot execute this desired result, because the alignment must be the same for all the presses, both precise and repeatable every the time.
Theoretically it would be necessary to verify ALL the cylinders for ALL presses, and subsequently realign ALL the printing decks on the same unique reference points ! This would be virtually impossible in the reality!
So, HOW to obtain a unique alignment suitable for ALL the cylinders for ALL affected press?
The answer is: with our mounter.
Our mounter is perfectly mechanically aligned on to the MASTER cylinder. Making it possible to have a specific alignment for each series of cylinders, enabling the customer to load the proper set up parameters before mounting.
The mounter becomes an affordable and unique reference for all the presses in the pressroom: all the presses are now capable of achieving the same perfect register.
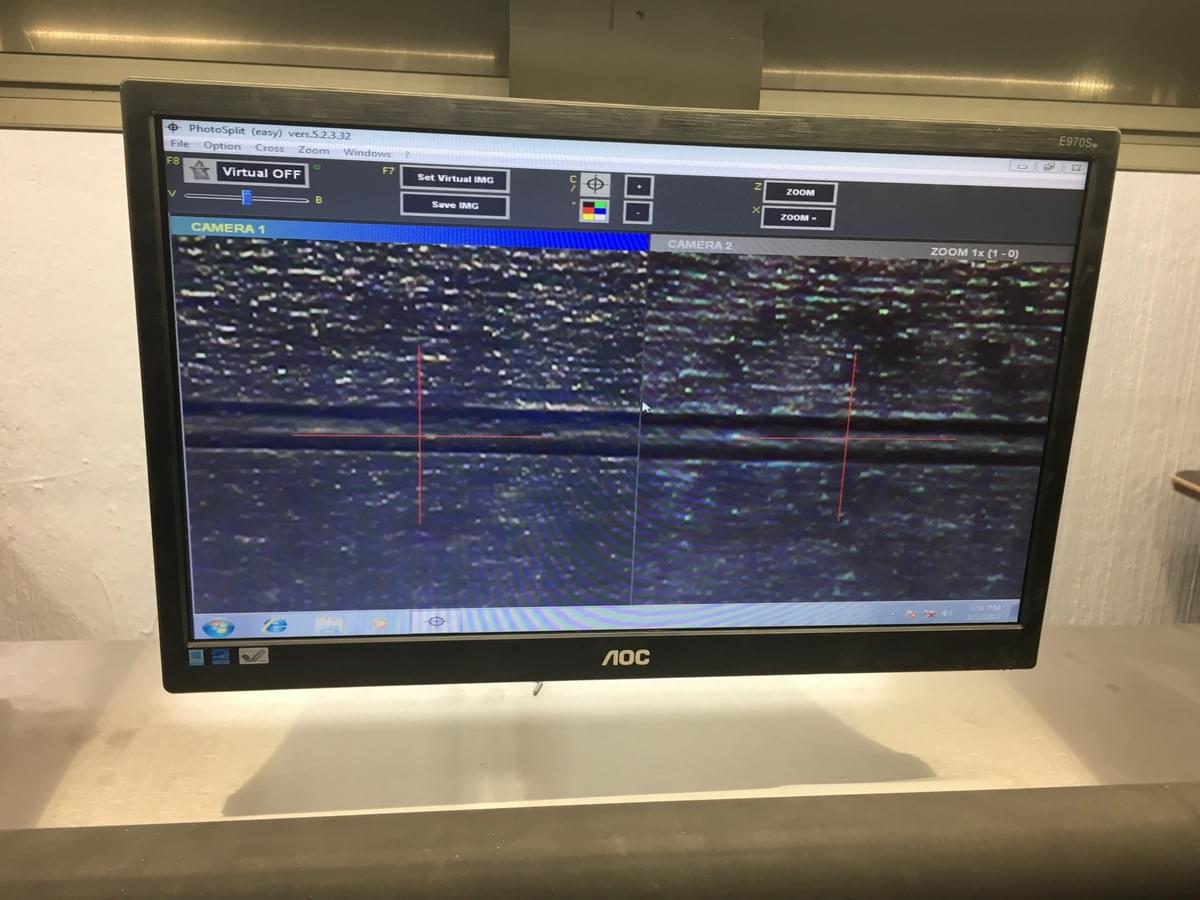
The concept behind our idea is that if the mechanics cannot be adjusted anytime (the purpose of the mounter is to be a constant and repetitive reference point in the time), then the software can compensate the mechanical gaps among the presses.
The MMP software function ("Moving and Manipulating the Pattern") allows the user to move the pattern (virtual air cross) on the screen, moving the crosses from the center of the video (theoretically the Cartesian coordinate "0.0") to any part of the video.
Moving the cross-hair, the operator can compensate for the "straightness" of each specific series of cylinders, for each press, obtaining the same precise alignment to the master cylinder used for the alignment of the mounter.
The process is simple:
- starting from the actual job that the operator assumes to be straight on a specific press
- this cylinder is delivered into the mounter, where it's immediately apparent if the cylinder is rotating exactly in the perfectly with the MASTER cylinder: the cylinder will be slightly misaligned compared to the theoretical scribed line engraved on the MASTER.
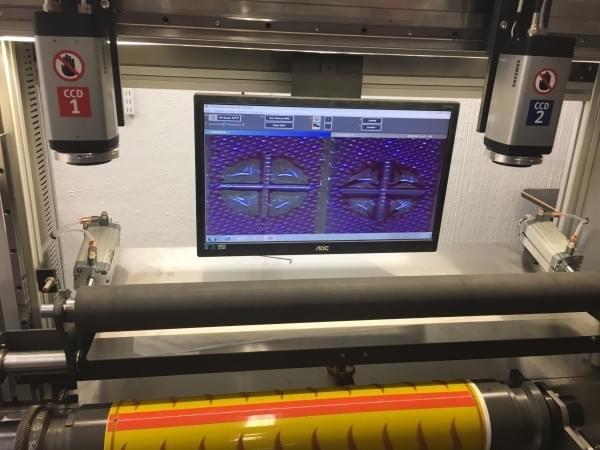
- at this point, the cross-hair can be moved by the operator until it matches the registry position on the exposed cylinder
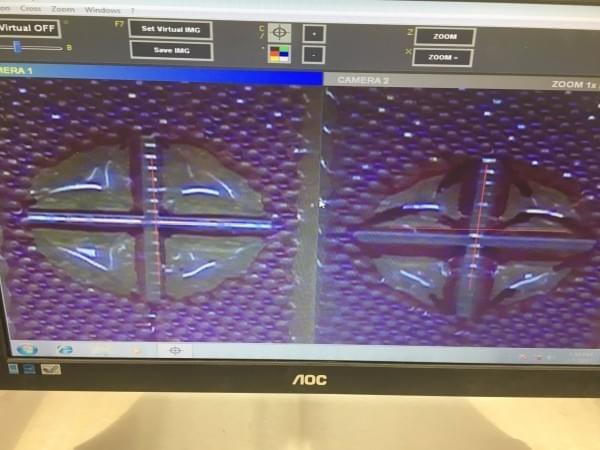
- this gap between the new position of the air cross and the coordinate "0.0" is the concentricity error between the cylinder and the MASTER.
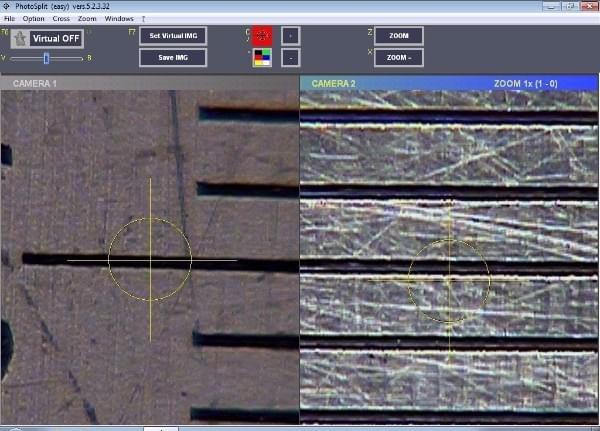
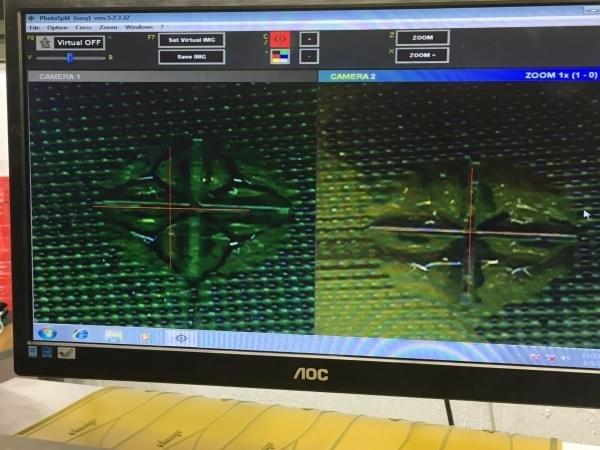
- the new position of the digitally generated cross-hair can be saved in the software, so it can be recalled when the same cylinder is mounted.
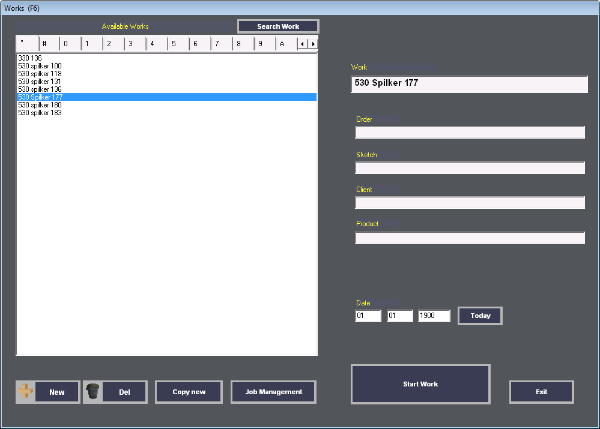
The MMP function allows a "controlled" misalignment of the machine, adjustable, verifiable, and repeatable.
The software helps to go beyond mechanical limits, and can give an added value to the operator in terms of flexibility of use of the machine, time and performance.
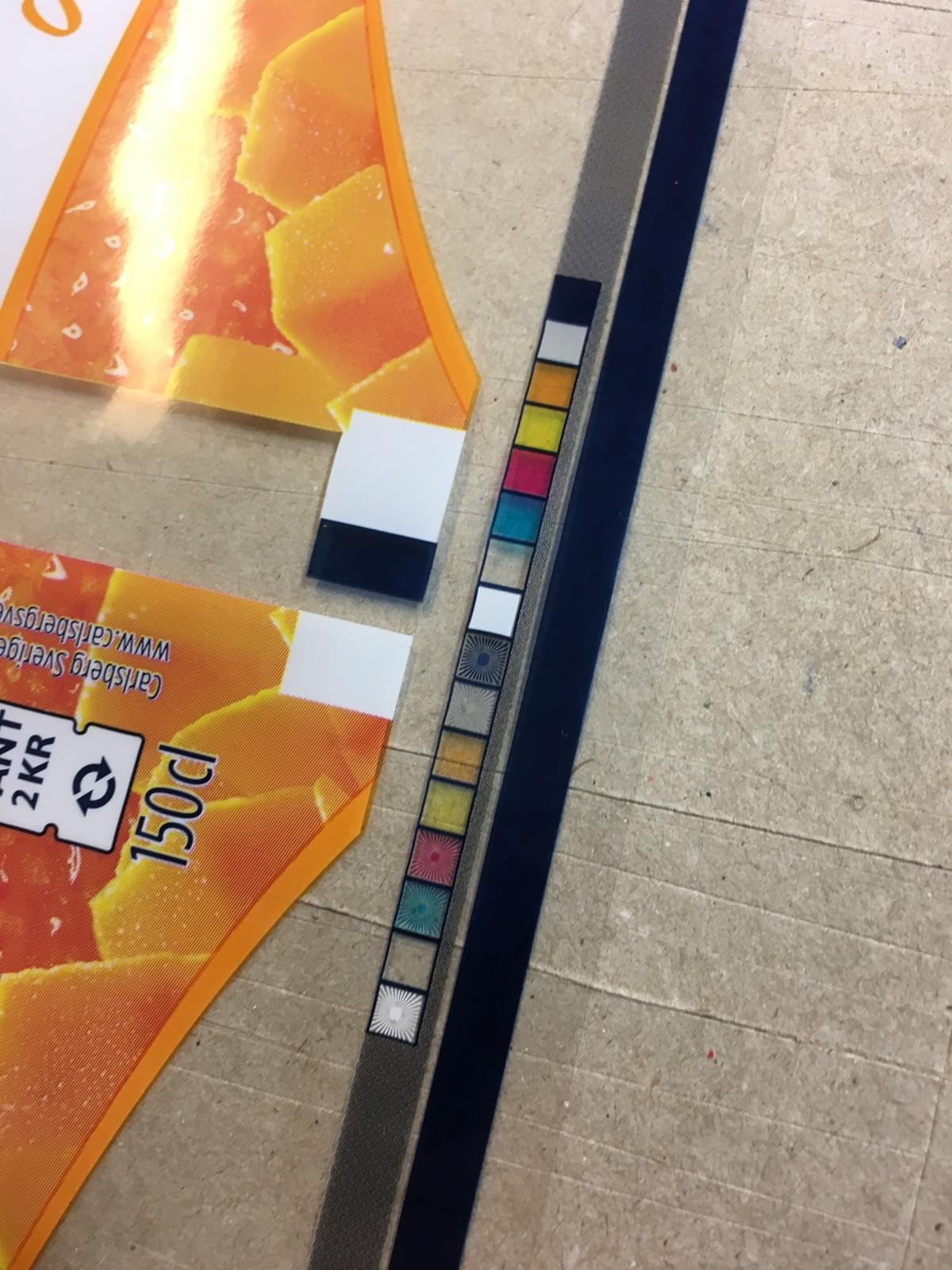
Author: Massimo Caliari (massimo.caliari@stconverting.com)
Thanks to Tim Reece (APR / Team Flexo) for the English revision